State-Of-The-Art Manufacturing Technologies
As our family of products has grown, so have our manufacturing capabilities for cab suspensions and heavy-duty truck suspensions. We have continued to expand our facilities and employ state-of-the-art manufacturing processes to build the most reliable and durable components in the market, ensuring our customers' overall products perform better.
Link always looks ahead, analyzing emerging manufacturing technologies to apply to future projects. Using lean manufacturing, we build suspension products on a larger scale to achieve manufacturing excellence and maximize the customer's value. We support our ability to deliver highly efficient manufacturing processes by investing in the highest-quality CNC bending centers, laser cutting systems, and powder-coat painting systems.
Our commitment to investing in quality and efficiency has also led us to achieve IATF 16949:2016 quality certification. This ensures we are able to fully address OEM requirements. The manufacturing processes we have put in to place also represent a commitment to environmental stewardship as highlighted in our ISO 14001:2015 certification.
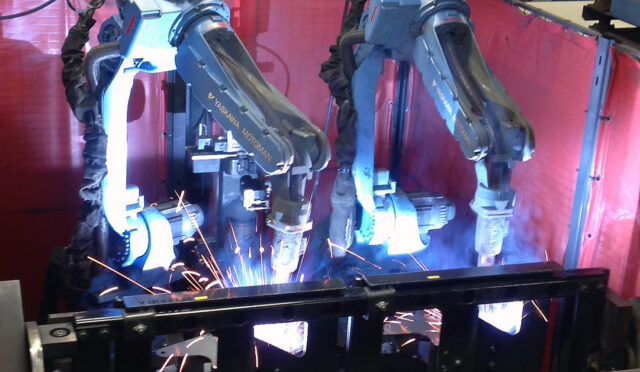
Manufacturing Technology
We incorporate new technology improvements to integrate seamlessly with your truck platforms for better performance. This includes single and dual head Motoman robotic welding systems, electrostatic powder coating systems, CNC controlled precision press brakes, vertical and horizontal machining, and CNC lathe. We fully embrace lean manufacturing using multiple high-tech automated CO2 lasers, a Bystronic Fiber laser and flexible continuous flow assembly, logistics centers, and other principles to ensure excellence.
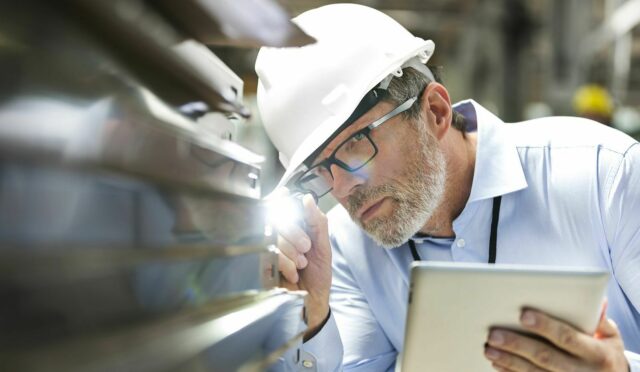
Focus On Quality
Our commitment to investing in quality and efficiency has led us to achieve IATF 16949:2016 quality certification. We fabricate and thoroughly test components to exceed rigorous OEM manufacturing standards. This attention to quality allows us to consistently achieve defective rates of less than 300 PPM. Our facility includes fatigue testing equipment; MTS component testing, MTS suspension performance testing, pull-apart testing, height control valve testing, and National Instruments data acquisitions equipment.
Contract & Military Manufacturing
We offer our contract manufacturing customers the ability to meet the unique needs for highly engineered, critical components for conventional, custom and military vehicle applications. Our engineering, design, suspension manufacturing and logistic teams collaborate with customers to bring precision into the project according to the product specifications. Overseeing each step of the fabrication process, our qualified staff and engineers work diligently to meet the high demands of each customer.