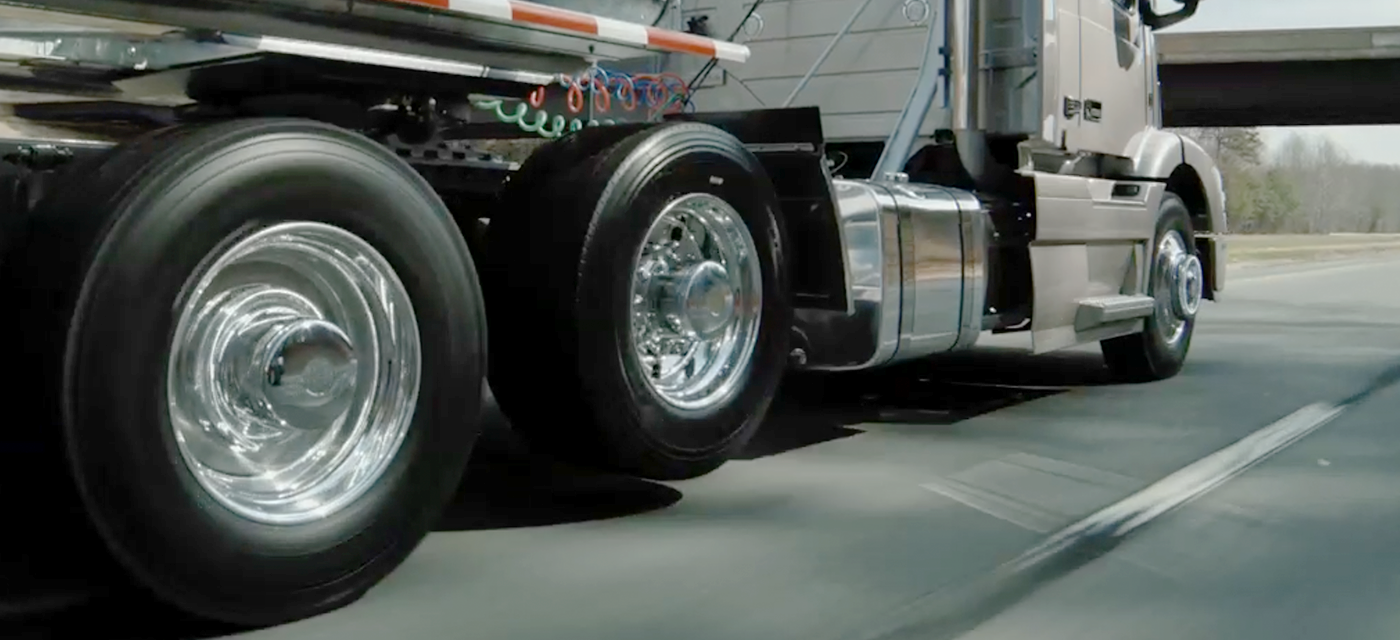
The Push for 6x2
If you were to look around highways in North America today, you will see more tractors with the traditional 6x4 axle arrangement than those without. However, you would likely also notice that some are running a slightly different configuration, the 6x2 configuration. The difference between a 6x4 configuration and the 6x2 configuration is that only one of the rear tandem axles has power in the 6x2, whereas in a 6x4 arrangement, both rear tandem axles have power. In Europe, the 6x2 axle configuration has become a more accepted format due to the arrangement’s substantial reduction in exhaust emissions. By 2027, the U.S. Environment Protection Agency suggests that the 6x2 adoption rate could increase to 30% due to upcoming greenhouse gas rules regarding fuel economy. While many fleets still use the 6x4 arrangement due to its prevalence, the 6x2 axle arrangement is gaining traction due to its many benefits to drivers and fleets.
The 6x2 Configuration – Drawbacks and Benefits
A 6x2 vehicle configuration typically utilizes 3 axles, a front steer non-driven axle, a rear driven axle, and a second rear axle that is non-driven. Fleets that use 6x2s in North America typically use a non-liftable dead tag axle, placed behind the drive axle. A tag axle always maintains contact with the road surface. While this is beneficial on dry roads, it can lead to insufficient traction by causing the drive wheels to spin on snow and ice-covered surfaces.
Typical 6x2 non-liftable, non-driven tag axle configurations are designed to add or remove suspension air pressure to the non-powered axle while maintaining or maximizing suspension air pressure on the drive axle. Additional air pressure in the suspension helps to provide traction to the drive axle. However, with the typical configuration, the non-driven axle still has contact with the road surface, which results in non-optimal traction. The load placed on the non-driven axle can adversely affect tire wear on the drive axle. Wear on the wheel ends may also occur due to additional strain of the equipment’s constant use. The non-driven axle causes additional rolling resistance, which limits the fuel economy benefits of the 6x2 configuration.
Introducing a liftable axle to a 6x2 configuration allows the possibility of lifting the axle when the tractor is in a bobtail configuration or connected to an empty or lightly loaded trailer. This can increase the traction of the drive axle when on the road, backing under a trailer on loose surfaces or while traveling on slick, icy or snow-covered surfaces. By lifting the axle, tire wear is reduced, minimizing unnecessary tire to ground contact. This reduces wear due to tire scrub. Wear and tear on the wheel ends and brakes can be reduced with the reduction of time that the axle is in use. By reducing the additional drag from the non-driven axle, fuel economy can be improved by up to 2% when compared to a non-lifting tag configuration.
By utilizing a 6x2 configuration with a non-driven axle, a tractor’s weight is reduced by up to 300 lbs. The 6x2 axle configuration eliminates the inner axle differential, ring and pinion, and the intermediate drive shaft. By taking away these elements and cutting back the overall vehicle weight, the load carrying capacity is increased. Weight reductions combined with reduced tire scrub, roll and parasitic drag result in as much as a 3-5% improvement in fuel economy.
Deciding Which Axle to Lift – Forward or Rear
Weight load distribution plays a large role in determining the placement of the lift axle. Typically, the ability to lift the forward tandem axle is the favorable option. The 5th wheel, or kingpin, is placed between the forward and rear tandem axles. If the rear tandem axle was to be lifted, the load from the kingpin would cause a cantilever effect behind the forward tandem axle, removing a portion of the weight load from the front steer axle. By removing a portion of the weight load from the steer axle, a negative impact occurs on steering control, making it more difficult for the driver to maintain a desired level of control.
If the forward rear axle was to be lifted, then no cantilever effect would occur. Instead, the weight is distributed between the rear axle and the front steer axle. A minimal portion of the load is transferred to the steer axle, limiting the potential that the axles will be overloaded if the rest of the chassis components are correctly spec’d. By placing the lift axle in the forward rear position, the 6x2 configuration will have optimal weight distribution between the rear-most axle and the steer axle.
Link’s Solution
Link has been at the forefront of the 6x2 movement, working with Volvo® on its 6x2 axle configuration. Working closely with Volvo and Mack engineers, our 6x2 pusher axle integrates with Volvo and Mack adaptive loading systems to help trucks run at peak fuel efficiency and performance. The system provides greater fuel efficiency by sensing weight differentiation and automatically lifting the auxiliary suspension when it is not needed, reducing friction and saving fuel when running lighter loads.
If you have any questions about our 6x2 lift axles, please let us know. Our team will be happy to answer your questions and put you in touch with a dealer near you.
Blog Author
Mark Molitor
Senior Product Manager - Chassis Suspensions
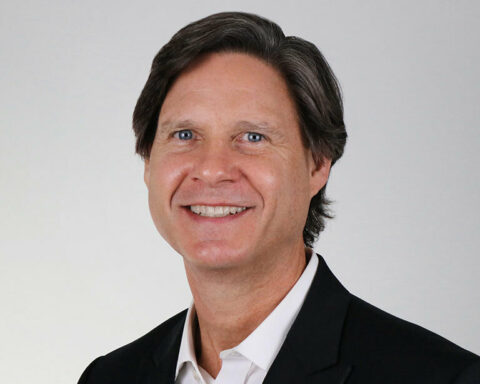